Introduction
Working in safety-critical industries such as construction and shipping involves many risks. If left unattended, these risks can lead to severe incidents that may result in loss of life, property, and harm to the environment. We need to reduce risks to prevent incidents.
We reduce risks through control measures. Control measures can be considered as barriers to incidents. An effective control measure eliminates or reduces the risk to a level where it is no longer a concern. But not all controls are the same. Some controls are more effective than others. Team leaders are responsible for implementing effective controls to the fullest extent possible.
The hierarchy of controls helps in understanding the different types of controls. Let us explore what it is.
What does the Hierarchy of Controls mean?
The hierarchy of controls categorizes control measures and arranges them in order of effectiveness. The graphical representation is shown as an inverted pyramid. The category at the top has the most positive impact on safety, and the impact reduces as we move from the top to the bottom.
The five categories are elimination, substitution, engineering controls, administrative controls, and personal protective equipment.
As per the hierarchy, we can have the highest positive impact on accident prevention by eliminating as many hazards as possible. If there are no satisfactory solutions and the risk remains high, we move on to the second stage, which is substitution, and so forth.
They redefine safety priorities by shifting the burden of accident prevention from the workers to system design. Research shows that such a shift offers the best system performance in terms of safety incidents.
Types of Controls
In this section, let’s delve deeper into the various types of controls available to us for risk management.
Elimination
Elimination is the most effective control measure. It is, therefore, also the most desired type of hazard control. In elimination, we try to remove the hazard. If there is no hazard, there is no associated risk. The operation becomes safer with every eliminated hazard.
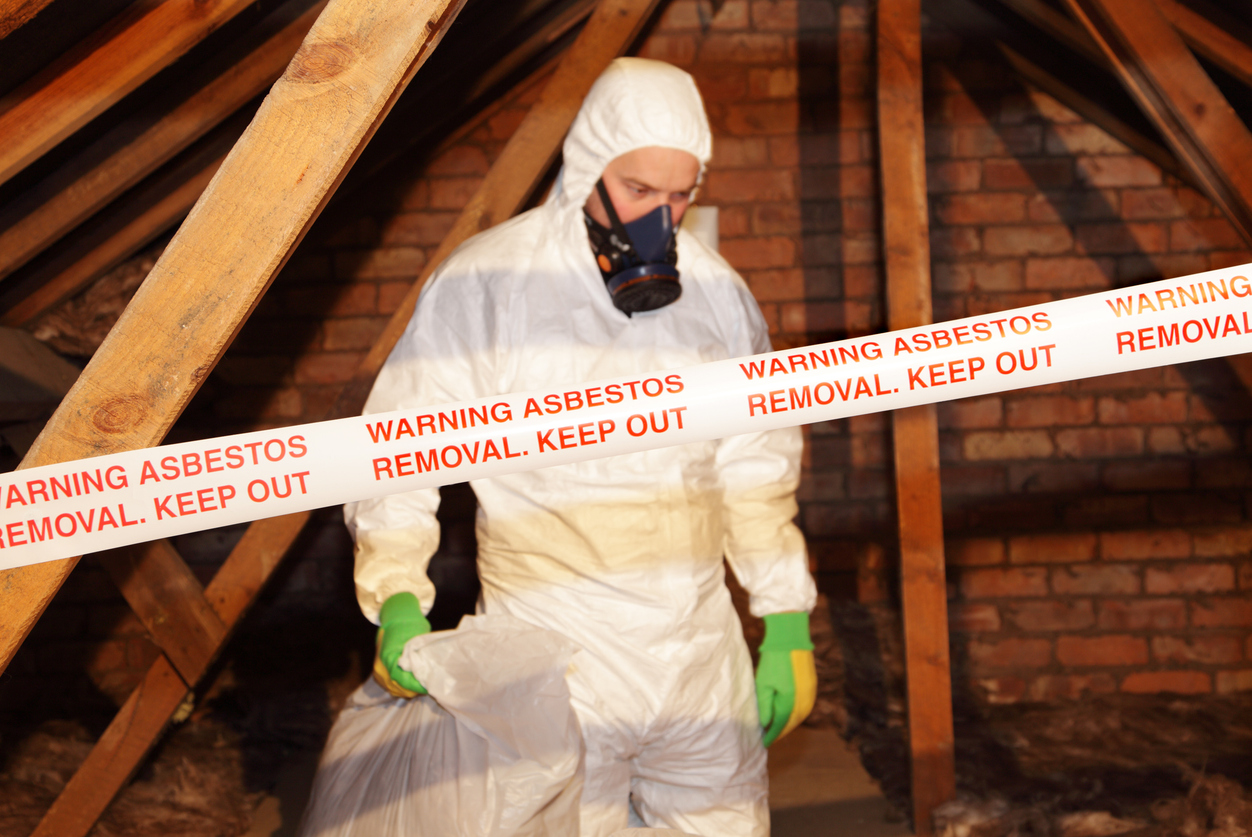
A worker wearing protective clothing while clearing the hazardous substance, asbestos, from a storage unit.
Elimination control examples
-
If a power tool is too noisy, we can rectify the fault or replace the tool.
-
When painting a ceiling, use a longer paint roller to paint from the floor. By doing this, you can avoid using a ladder to reach the ceiling with a shorter roller.
-
The removal of hazardous waste from storage and disposing of it properly.
-
Ensuring personnel stay clear of snapback zones during mooring operations.
-
Replacing faulty electrical devices with new ones can help eliminate the risk of shock or short circuits.
-
Replacing worn-out harnesses and safety gear with new equipment.
-
Elimination of pinch points by increasing clearance.
-
The use of cordless equipment helps eliminate cables on the floor.
-
Smoothing out elevation changes to prevent tripping.
Substitution
If eliminating hazards is impossible, we must try substituting them with less hazardous alternatives. We may also change the form of a substance if it reduces the hazard’s risk. For instance, wherever possible, we must try to eliminate the use of toxic chemicals by replacing them with non-toxic alternatives.
Substitution control examples
-
If a process involves using a chemical in dust form, we can opt for pellets instead to minimize the risk of inhalation hazards.
-
Switching to water-based paints instead of solvent-based paints. Utilization of acrylic paint instead of lead-based paint.
-
Installation of slip-resistant flooring in high-risk areas.
-
Bending metal in a vice instead of hammering it into shape.
-
Replacing latex gloves with non-latex gloves.
Engineering Controls
An engineering control is a change in system design that prevents workers from being exposed to hazards. We place physical or operational barriers in the process to prevent incorrect operation or accidental contact.
These types of controls are sometimes also known as isolation controls. For instance, when we need to work on hazardous equipment, such as steam lines, we shut the steam inlet and outlet and drain the steam and condensate, and isolate the section before starting work.
Engineering controls examples
-
Cordoning off areas where a manhole has been opened.
-
Erecting enclosures around high-voltage equipment.
-
Shifting the control of machinery to a remote location to prevent accidental start/stop.
-
Placing “Men at Work” notices at all positions from which a piece of equipment can be operated.
-
Installing guard rails in areas where there is a risk of falling.
-
Warning notices about pinch points and the use of pinch injury prevention gear
-
Encasing noisy machinery in a soundproof enclosure
Administrative Controls
Administrative controls refer to procedures and policies implemented to protect workers from workplace hazards. They involve measures such as modifying work practices, regulating entry into hazardous areas, using warning signs/posters, checklist-based operation, etc.
Administrative controls examples
-
Before starting jobs, workers ndeed to fill out isolation permits, hot work permits, working at height permits, and enclosed space entry permits.
-
Placing warning signs outside of hazardous areas to inform workers about hazards and recommend control measures
-
Implementing a system where workers notify individuals outside the hazardous area before entering for work tasks.
-
Implementing a preventive maintenance system to ensure that machines are maintained in good working order.
-
Setting up work schedules to minimize the duration of exposure to a hazard.
-
Postponing hazardous maintenance processes and operations to times when occupancy is low, such as after work hours or weekends.
Personal Protective Equipment (PPE)
Personal protective equipment, or PPE, is the last line of defense against safety incidents. If all the other controls are implemented effectively, we may not need PPE at all. But this is not usually the case. All tasks, despite effective control measures, carry a degree of risk. Thus, while PPE is the last type of defense, it must be used diligently to prevent safety incidents.
There is almost always some deviation from work procedures regardless of the task. Safety approaches define this as the difference between Work-as-Imagined and Work-as-Done. When we imagine work, we do not expect mistakes or forget important steps. But when the work is actually done, this can happen for a number of reasons.
Such deviations from procedures require the implementation of additional control measures as the risk increases. Personal Protective Equipment (PPE) is one such control measure.
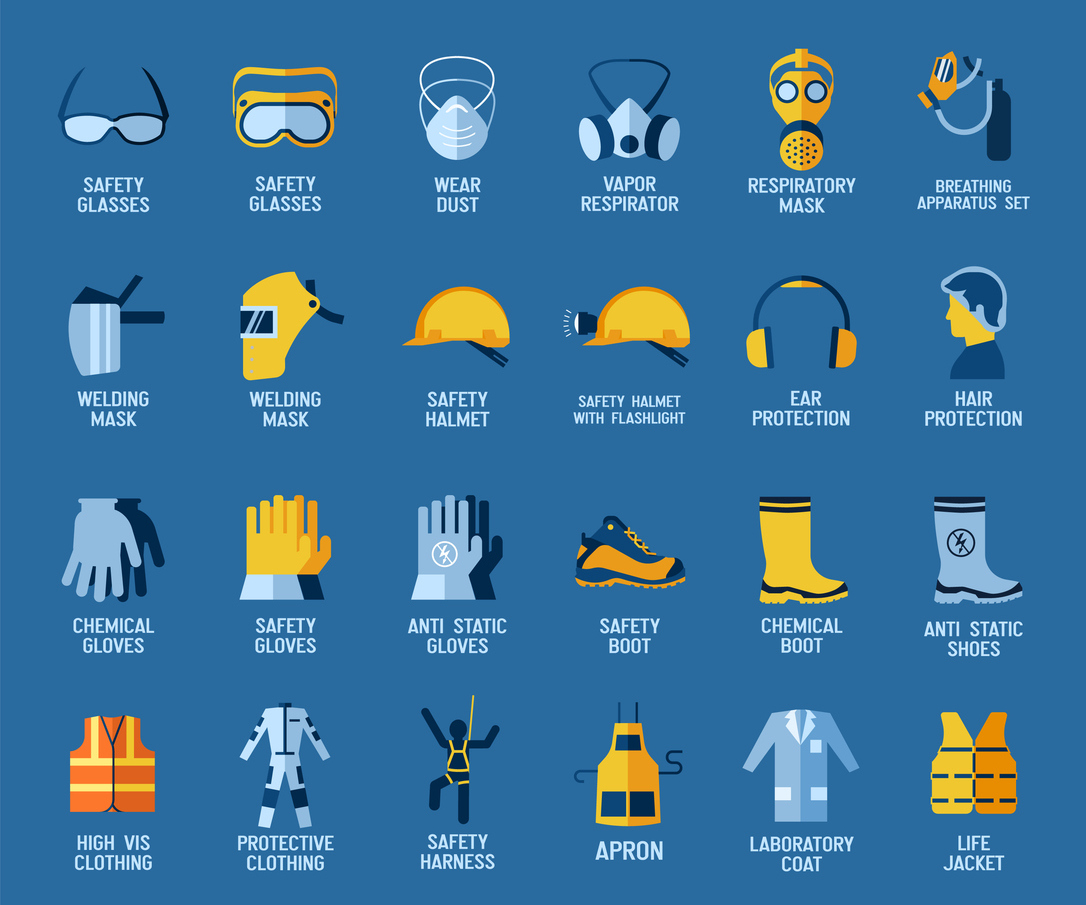
Personal protective equipment examples
-
Helmets should be worn in open areas where there is a risk of falling objects. This could occur during cargo discharge operations on ships or maintenance in factories. The construction industry also requires the use of helmets at worksites.
-
Use of chemical gloves even when handling sealed chemical containers
-
Eye protection through safety goggles or face shields when using power tools or working near flying dust, debris, and other objects.
-
Other forms of PPE include safety shoes, boiler suits, breathing apparatus, ear muffs, personal gas meters, harnesses, lanyards, etc.
FAQ
Who developed the Hierarchy of Controls?
The National Institute for Occupational Safety and Health (NIOSH) developed the Hierarchy of Controls. It is a U.S. federal agency that conducts research, develops recommendations, and establishes safety practices to protect workers. The aim is to provide a safe work method and a safe work environment.
When should the hierarchy of controls be used?
The hierarchy of controls is applied after identifying all the hazards. We adhere to the hierarchy and select appropriate controls to mitigate the risk of hazards.
What are the 6 hierarchy of controls?
Some systems have an additional type of control known as isolation between substitution and engineering controls. This control refers to measures that separate the hazard from those at risk. In the 5 hierarchy of controls system, isolation measures are included in engineering controls.
Leave a Reply